A small aerospace component manufacturer of precision electro-mechanical devices had a long-established fabrication and assembly process that was creating repetitive motion injuries in its’ highly-skilled and experienced workforce. A detailed process and workflow analysis revealed the time-intensive (up to 45 minutes per unit, often more when including rework) fine motor skills required to create the product to be the root cause of the injuries and lost-time. The existing process and product design demanded the longstanding and expensive “hand-crafted” approach be used to get a durable precision finished product. However, the customer valued the functionality, precision, and durability…not the “hand-crafted” process. In order to address the injuries and high labor content, a wholistic approach to problem-solving revealed, with some minor material changes, reduction in BOM components, and improved assembly process, the end product was able to be produced with 75% less touch-time, 10% fewer parts, 80% less rework, higher durability, and increased strength. The repetitive-motion injuries and this production bottleneck were eliminated, increasing production output by 45% using an off-the-shelf bench-top assembly technology with a 3 month ROI.
Injuries, high rejects, and/or the requirement for exceptionally highly skilled labor can all be indicators of improvement opportunities, even in long-standing or “proven” products/processes. Let Leanpathdirect help you identify your next game-changing improvement.
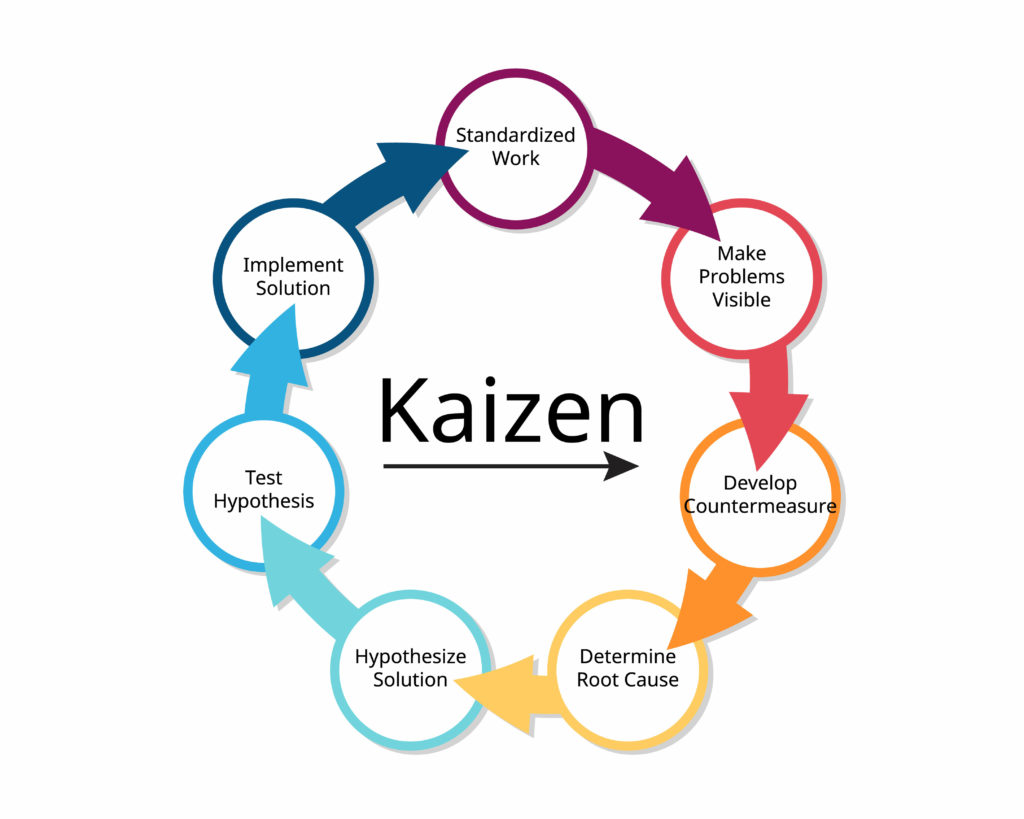